Anti-lock brakes have been a staple of automotive safety for the last twenty years. Not only is it federally mandated, but it's difficult to find a vehicle without it. Driving with anti-lock brakes adds an enhanced level of safety in all conditions, whether it be winter, spring, summer, or fall. The best part about ABS is its transparency to the driver - there are no buttons, switches, or settings at all, in nearly every car on the road today.
This transparency has been achieved through years of innovation and progress to make anti-lock brakes as reliable and dependable as they can be. In an emergency a driver wants one thing: Full braking force, right now. Since braking force is often determined by road surface conditions, it is logical to want as much braking power as the surface provides in a way that maintains full car control. Simply locking up the brakes in a non-ABS equipped car may work great on a hot dry day, but paint a grim picture in the rain or snow. Modern anti-lock brakes solve this problem by doing the work of four individual brake pedals, when the driver only has access to one.
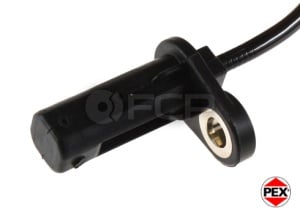
How ABS Sensors Work
PEX passive ABS sensors use OE grade wiring and construction. Ever install a speedometer on a bicycle? A tiny magnet mounts to a wheel spoke, and a wired sensor straps on to the front fork. Each time the magnet passes the sensor, the computer picks up the signal and translates the frequency into a speed reading. A passive ABS sensor works in much the same way, but with more ruggedized components and the sensor itself housing a magnet.
Inside this PEX sensor is a magnet, wrapped in a copper wire. Typical on passenger cars, a toothed wheel (sometimes called a tone ring) is mounted on the axle shaft. As this wheel spins closely past the ABS sensor, an AC voltage is generated, creating a sine wave pattern picked up by the ABS module. The module interprets this pattern as the speed that particular wheel is traveling.
A dirty ABS sensor or cracked tone ring can wreak havoc on an ABS system, creating false engagements or error codes that prevent the system from engaging entirely.
However, all four wheels are not expected to be traveling at the same speed at all times. While turning through a sharp hairpin turn, the inside wheels will be spinning slower, and the ABS module knows that. There is always a tolerance at which the wheels can differ in speed before the vehicle thinks a problem is looming. In a panic stop situation, the difference between wheel speeds can be over 30 miles per hour, indicating a locked wheel and the need for anti-lock brakes at a moment's notice.
When a wheel locks up for even a split second, valves in the ABS pump's manifold reduce pressure to that wheel's brake caliper in a fashion that keeps the wheel as close to the threshold of lockup as possible. Since a rotating front wheel allows a vehicle to be steered more than a locked wheel, the usefulness of ABS is realized immediately.
Passive and active
Utilizing two wires, a passive ABS sensor creates an AC current that is seen as a sine wave in the ABS module, then converted to digital. The tone wheel has ridges that come very close to the sensor's magnet, effectively "blipping" it into producing a voltage the ABS computer recognizes. Two disadvantages to passive sensors are their inability to produce a clean signal under 5mph, and the vehicle's inability to decipher which direction the wheel is traveling.
Active ABS sensors typically use two or three wires and eliminate nearly all the shortfalls of passive sensors. Though they are more compact, active ABS sensors can accurately measure speeds of less than 1mph and produce a forward and reverse wheel speed signal for the ABS module. A two wire active sensor uses one ground and one reference voltage wire, with the signal traveling on the reference wire. Three wire active sensors use separate ground, reference voltage, and signal wires.
Active (or hall effect) sensors always send the same exact signal amplitude back to the ABS module, with a varying frequency in square wave form. Passive sensors produce a varying amplitude sine wave signal that only begins at a certain speed, making active sensors the choice of vehicle manufacturers since 1998.
ABS System Types
Although the ABS systems of yore maintained the same intention as they do today, there were various methods in which the systems worked, some being more effective than others.
A typical MY2015 vehicle is equipped with a 4-channel, 4-sensor ABS system. The system uses four sensor inputs to gather data from each wheel, and can modulate four brake channels individually. If the left rear wheel locks up in a skid, the ABS module can reduce brake pressure to the threshold of lockup on that single wheel to keep the vehicle stable, moving in the driver's intended direction.
Older systems like on the 1997 Volvo 850 utilized a 3-channel, 4-sensor ABS system. If either of the rear wheels locked up, both wheels would be modulated by the ABS pump in tandem as they are supplied brake fluid by the same channel. In this configuration, a single brake line runs to the rear of the vehicle where it is split at the rear axle to each caliper.
A 3-channel 3-sensor system typically utilizes two sensors on each front wheel, and a single sensor inside a fixed rear axle to measure the speed of the differential. Only the two front wheels can be individually modulated, and both rear wheels would need to exhibit lockup for the rear brakes to receive any anti-lock function from the ABS system.
4-channel 4-sensor systems have obsoleted previous styles due to the necessity of advanced traction and stability controls, and increased demand from consumers who want the safest possible vehicle. Without the ability to modulate each wheel individually, stability and traction control systems could not function to their fullest potential, and new vehicles would not meet the strict safety standards of modern times. Other systems with less sensors and less controllable channels have also existed, but 3 and 4 channel/sensor systems have been the most common in the last few decades.
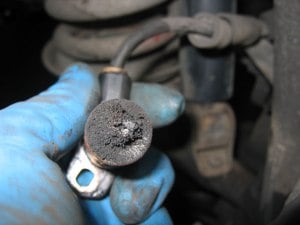
How to clean a sensor
ABS sensors are magnetic, so it is only natural for them to pick up particulate metal debris as they age. An on-car brake lathe is the most usual suspect for producing a high level of metal shavings that would cause an immediate issue. No worries - an ABS code tripped from a dirty sensor is the best possible scenario and will only cost a can of brake cleaner. I typically use aerosol brake cleaner spray as it evaporates quickly and keeps harmful brake dust from becoming airborne. Wipe the end of the sensor with a damp rag. This ensures the most accurate speed reading and decreased likelihood of ABS codes.
When replacement is needed
Moisture, age, and vibration are among the three most common reasons an ABS sensor will fail. Cracked wiring from road debris or ice can split or corrode from moisture intrusion. A cracked sensor body will allow moisture in and fail due to compromised copper windings. Most ABS sensors are located in hot, dry areas like the knuckle or hub - two things that plastic sensors can only tolerate for so long.
Replacing an ABS sensor is often one of the easier tasks to perform on a European car. Fastened with just one bolt, replacement only involves wheel removal and un-routing the sensor wire from its mounting points. To see how easy it is to replace a front left ABS sensor on a 2007 BMW Z4, see the video from FCP Euro below.